Production Environment
- Homepage
- Production Environment
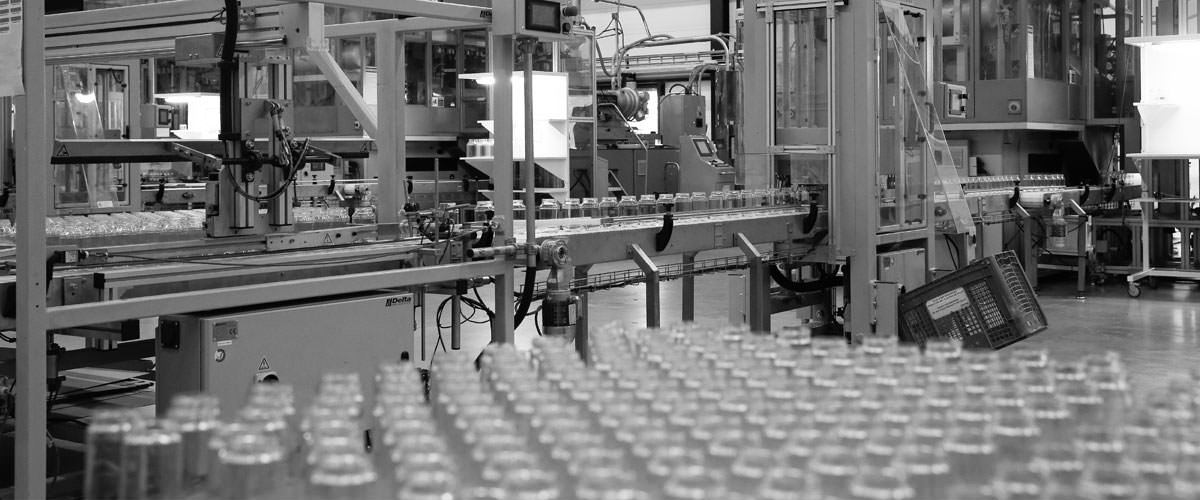
HIGH TECH PRODUCTION ENVIRONMENT
As a customer, you want to choose a partner who can guarantee a stable and consistent quality of PET bottles and containers. Thanks to its advanced production lines, Can Pet can meet almost all customer requirements. We also regularly invest in the latest injection stretch blow molding machines, automation and inspection equipment. We continuously improve our production processes by applying the LEAN production philosophy and Sigma 6 projects.
High quality raw materials
The same approach is reflected in the selection, purchase, inspection and use of raw materials and additives. Suppliers are regularly reviewed and audited. We conduct strict inspections on incoming goods and ensure that our products comply with agreements with our customers during the production process. As a member of Berry, we have long-term relationships with leading PET and other raw material suppliers. There is always enough material of sufficient quality to produce and supply your packaging quickly.
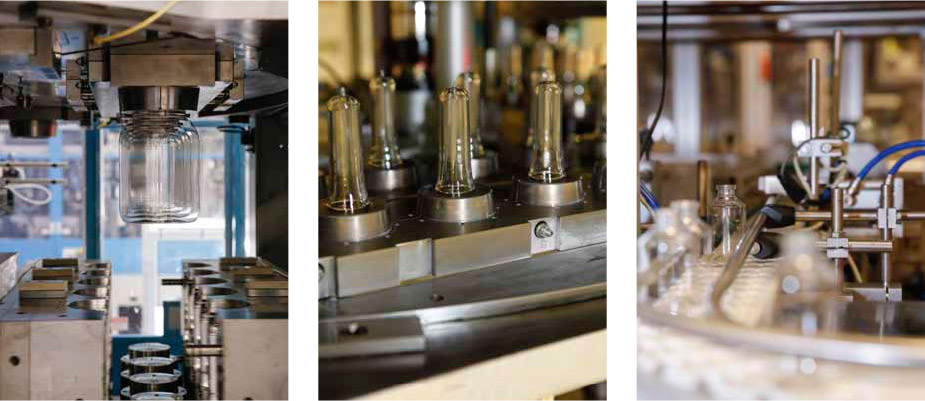
3 STEPS TO PERFECT PET PACKAGING
Can Pet mainly uses the ISBM production technique (Injection Stretch Blow Molding). Most of the production is produced using a one-stage technique. In this technique, a single machine produces both the preform and the final PET bottle or container. This method is quite suitable for both small and large series. The process is divided into three steps.
Stage 1: preform
PET granule (raw material) is dried. It then passes through a screw-shaped cylinder in the dryer to the machine. During transport, the granules are heated, resulting in liquid PET. In normal PET, glassy clarity occurs at this stage. Colored material is obtained by adding coloring agents when necessary. The liquid mass is then injected into the first mold: the so-called preform mold. This way, the neck of the bottle or container will get exactly the right size and the entire bottle or container will get the right weight in one go.
Stage 2: final form
The preform will now receive a high precision blasted neck. The preform is then placed on a turntable and transported to the next station. On some machines this is a station for conditioning this preform, for example to further optimize the temperature profile. On other machines this preform is transported directly to the blowing station. The blow mold gives its final shape to the front mold by blowing and stretching the flexible part under the neck. A rod-like blow pin is inserted to stretch the material to the bottom. The blowing technique allows PET to be pressed against the edges of the blow mold, which can result in all sorts of shapes and patterns.
Stage 3: finished product
The same approach is reflected in the selection, purchase, inspection and use of raw materials and additives. Suppliers are regularly reviewed and audited. We conduct strict inspections on incoming goods and ensure that our products comply with agreements with our customers during the production process. As a member of Berry, we have long-term relationships with leading PET and other raw material suppliers. There is always enough material of sufficient quality to produce and supply your packaging quickly.